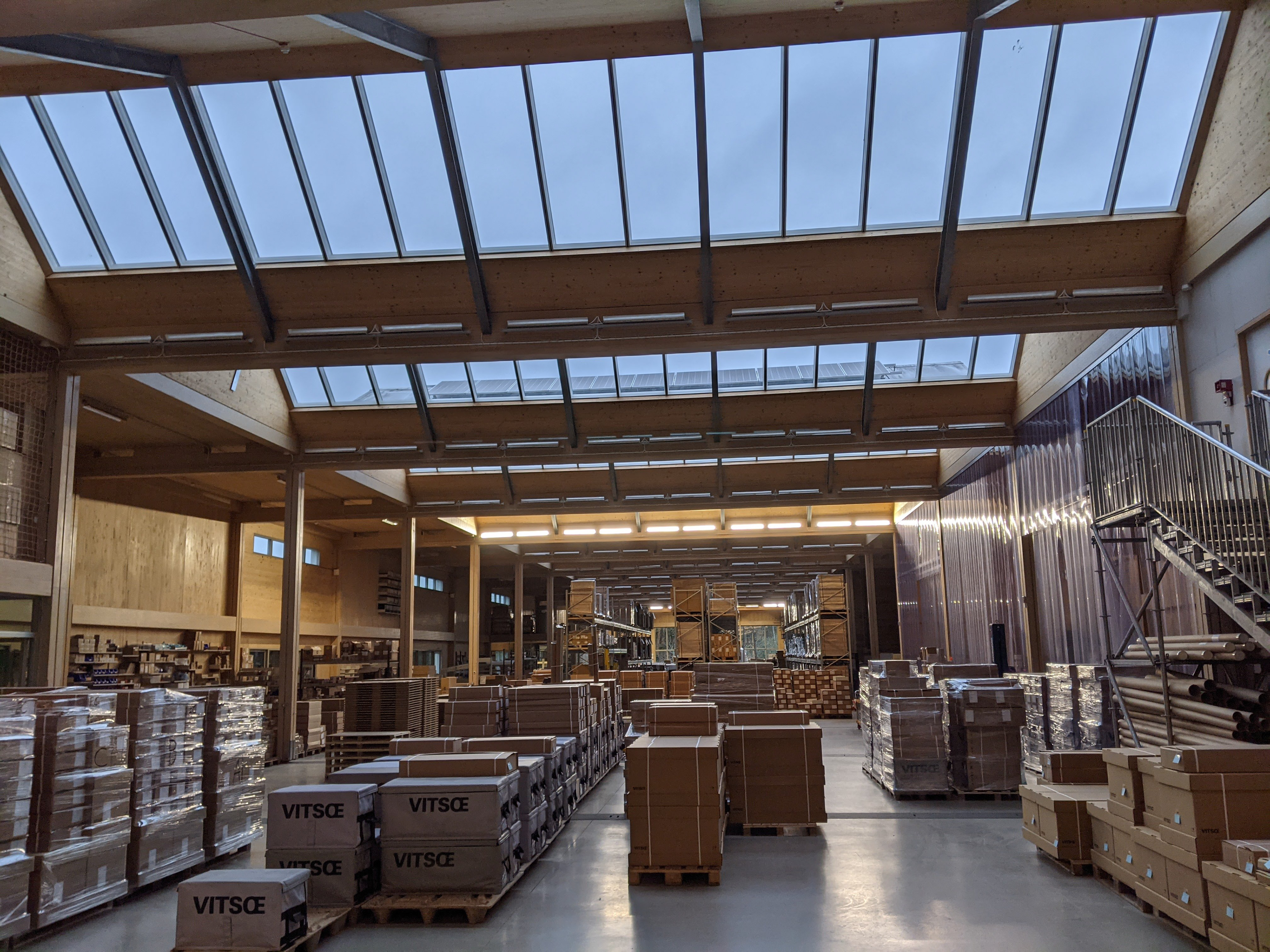
For the placement year of my degree, I found employment with Vitsoe.
Vitsœ is a company that has made the same selection of Dieter Rams furniture for 65+ years, so as you can imagine they are doing something right.
I joined their team in Leamington Spa in December of 2020 which is when companies with suitable work conditions were able to have workers come back from furlough so there was a shortage of staff in a number of departments initially so I was able to be applied in a variety of roles as support.
I began by working with wrapping, checking off and loading shipments onto containers while liaising with drivers, assisting with labelling, packaging and preparing orders going around the globe.
My responsibilities and roles expanded as I progressed and learned the company.
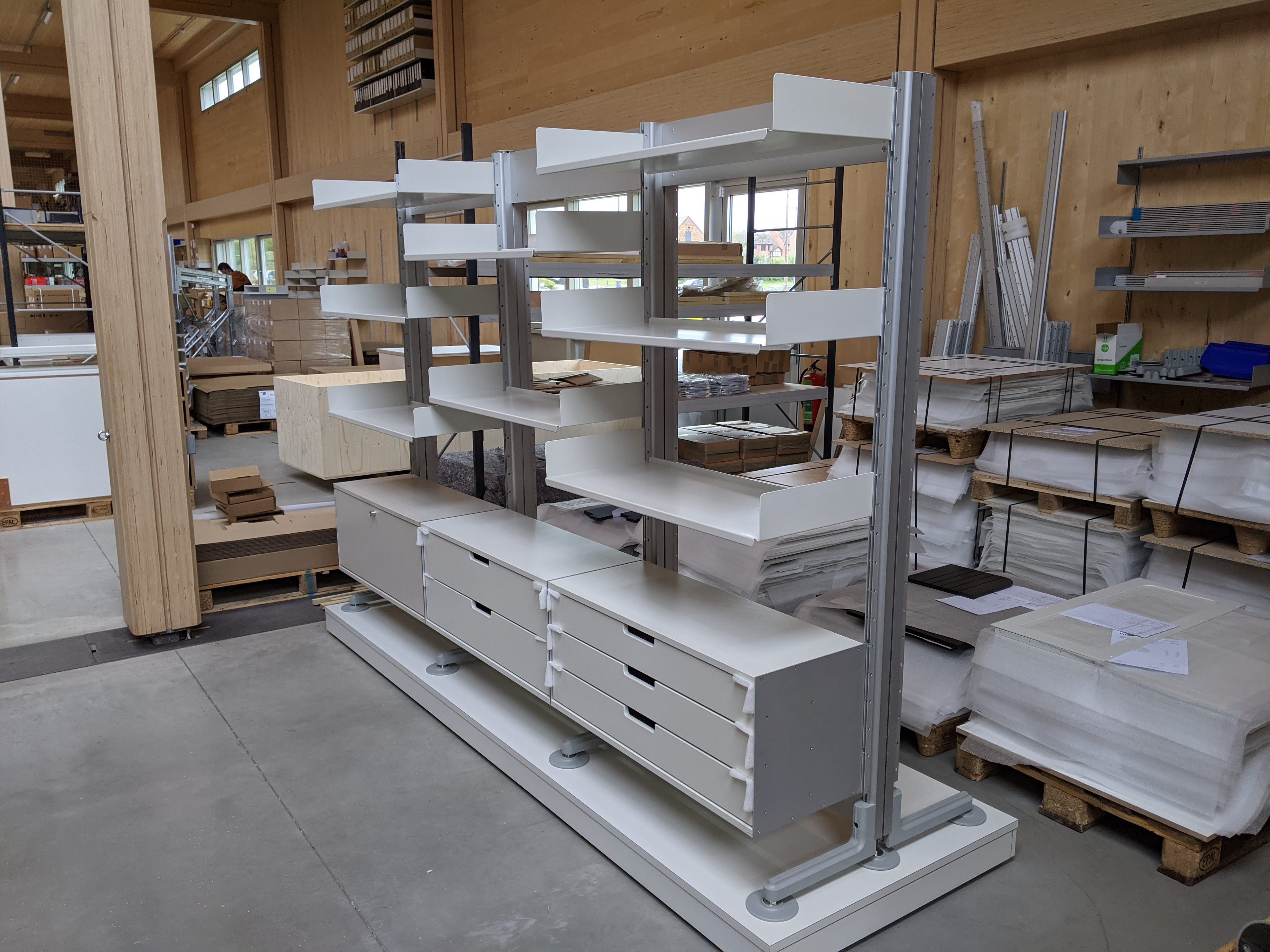

As my department leads trusted me more I was given significant jobs such as preparing display pieces for showrooms as well as orders worth greater than £100,000 one example is a presentation piece for Birkenstock's Paris shop was my responsibility to machine the metal components correctly and finish to an excellent standard.
These responsibilities enhanced my eye for cleanliness and presentation as well as improved my ability to be precise with extreme consistency.


Later in my time at the company, I was shown how to perform quality control for fibreglass components, these were the main parts of the chair sold by the company and many have visible faces that need to be scoured for any imperfections as well as prepared for powder coating in the next stage. This educated me on proper PPE as well as meticulous detail.
A continuation of the order for Birkenstocks that I was heading for was the interesting packaging solutions to cumbersome and awkward items with a high chance of damaging or gaining imperfections en route to the customer.

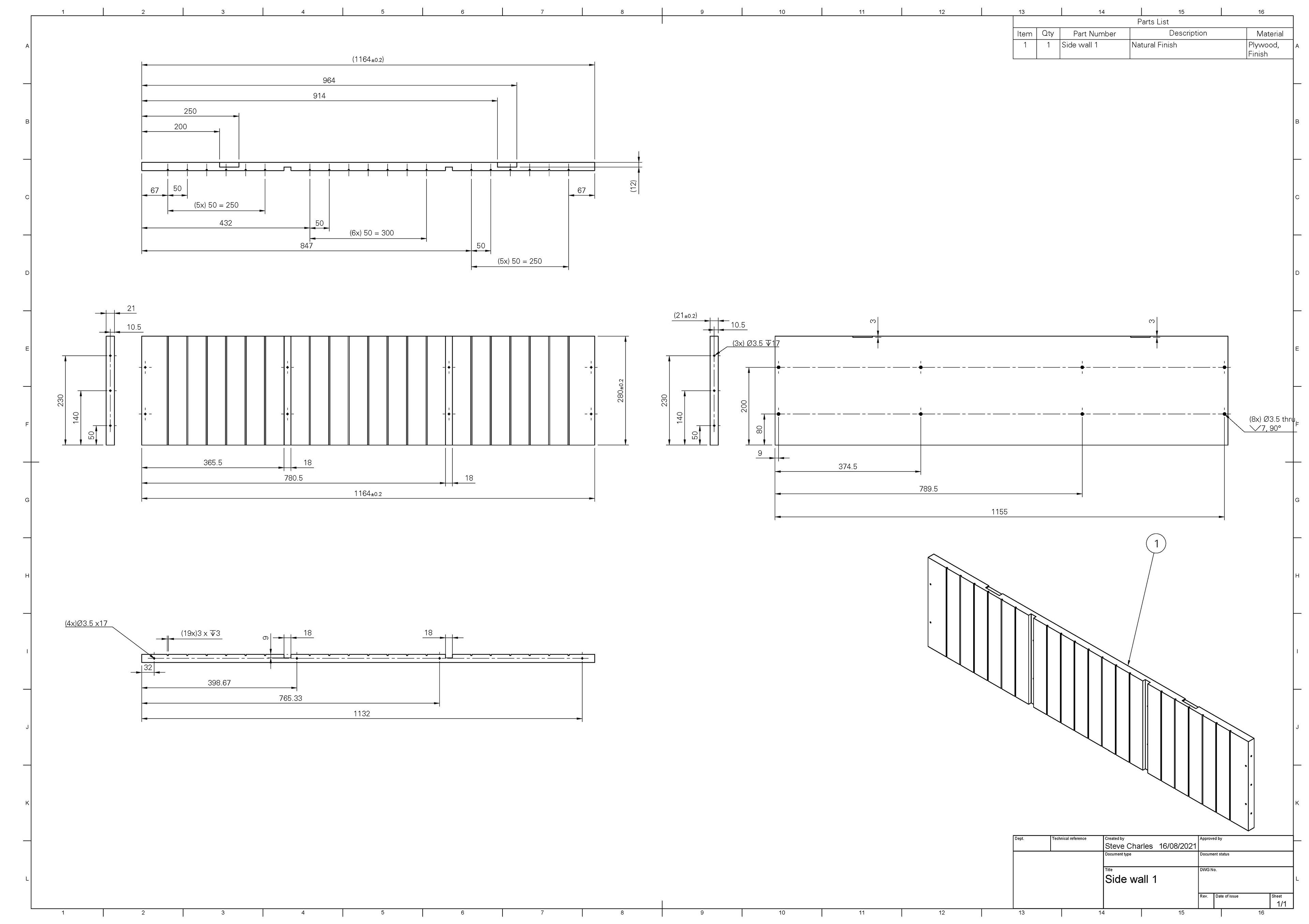
Here are a couple of the technical drawings that I made for a storage vessel for shelving components that would be sent between suppliers and finishing companies travelling from Germany to the UK and back. It was designed specifically to be palletised and thus is made to safely hold as many components as possible to keep transit costs to a minimum, these were completed within Fusion 360.
This industrial placement gave me the opportunity to have a unique perspective on an established and successful British design company, the decisions for the location of the HQ and then the carefully considered layout of the inside of the building. I was able to learn what to do as well as what to avoid when it comes to the satisfaction and validation of all employees as well as customers.